Powder coating paint shop
Qkomaxit s.r.o. is a powder coating paint shop located in western Slovakia in the village of Madunice. Our main focus is surface treatment and powder coating. The primary objective of the company is to meet the customer’s requirements to the maximum extent. We offer full technical support, quick turnaround on all our product orders. The high quality of finished product is improved by mechanical or chemical pre-treatment. High flexibility and speed of production enables a prompt response to every requirement of the customer.
Powder coating and the Technology
Three-lane overhead conveyor with perpendicular sliding ramp
Gas furnace with two burners with maximum output of 160kW
6m long Spray booth, for two persons with air freezer
ATLAS COPCO 54kW compressor with air freezer
Maximum dimensions of painted parts are: 6.0 x 1.8 x 1.5 (L x H x S [m])
The maximum weight of painted parts in our paint shop is: 1500 kg
SAND BLASTING
Blasting – surface treatment by blasting belongs to a very common surface treatment before its final treatment. Blasting (pneumatic, compressed air) refers to the treatment of a surface by a jet of a blasting (working medium), to which it usually supplies compressed air with motive energy. At the same time, there are several accompanying phenomena during blasting, which have a significant impact on the quality of surface finishes:
- Mechanical removal of the top layer of material that is contaminated, attacked by corrosion and is inconsistent - i.e. its chemical composition is not quite typical of the material. The reason for this is the presence of inefficient oxides that are produced in the production process (rolling, pressing, welding, etc.) and these make the material less consistent on the surface
- Roughening of the surface – this is created by anchoring profile - when viewed under the microscope, it has the character of sharp peaks. This results in a large number of slip surfaces which prevent peeling of surface treatments.
- Degreasing of the surface - during blasting the surface is heated and thus easier to remove the grease absorbed by the abrasive material and dust particles formed on impact.
Blasting mechanically removes scales, corrosion products and other contaminants from surfaces of various materials, creating a suitable surface for anchoring powder paints, paints, as well as hot-dipped metals (zinc, aluminium, zinacor 850, copper, bronze, brass, iron, stainless steel). Blasting is suitable not only for steel constructions, but also for other materials such as. concrete, cladding, wood, stainless steel, aluminium, stone, etc. Blasting has a decisive influence on the adhesion of the protective layer and thus indirectly on its service life.
CHEMICAL PRE - TREATMENT
The resulting quality of the cured coating is highly dependent on the chemical pre-treatment of the surface of the material before the paint itself is applied. Surface preparation of the material is carried out under different conditions for iron and others for aluminium. Phosphating is used for iron and titanium is used for aluminium. Both are applied by immersion in the degreasing solution, followed by rinsing in demineralised water and another immersion in the passivation solution, each submersion having its specified technological time and solution temperature. These are relatively complex processes to control the quality of each solution as they must be monitored daily. Phosphating is the formation of an intermediate layer (2-5 µm), which increases the parameters of the following operation, thus improving the adhesion of the applied powder and increasing the corrosion resistance. We are talking about iron phosphate, which can be applied to the surface of iron, steel, aluminium and galvanized surface.
Powder Coating
Powder coating of metals is a cutting edge technology that is already an essential part in the engineering and construction industries. It is a technology where powder coatings are applied by spraying in an electrostatic field. A common feature of all processes of this kind is that the powder particles are electrically charged while the painted object is grounded.
The powder particles are charged in two ways:
- electrostatic charging (corona charging, "STATICS"), passing the powder through a high-voltage electrostatic field
- tribostatic charging (friction, "TRIBO"), where the electrostatic charge on the powder particles results from their friction on the insulator.
The resulting electrostatic attraction force is sufficient to form a sufficient layer of powder on the article, keeping the dry powder in place until it melts and adheres to the surface in a special curing oven at a temperature of 170-200 ° C and at the required time of 10-25 min. With such surface treatment, the product has excellent chemical and corrosion resistance, impact resistance, abrasion resistance, flexibility and is also suitable for contact with drinking water, children, food, etc.
REFERENCES
PARTNERS
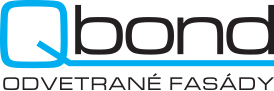
certifiCAtE
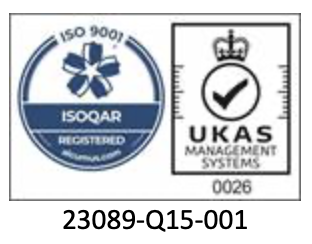
SEDN US A MESSAGE
CONTACTS
phone: +421 337 301 721
e-mail: info@qkomaxit.sk
Operating hours:
7:00 – 16:00
Paint shop:
Družstevná 12
922 42 Madunice
Slovakia
Billing info:
Športová 687/21
92207 Veľké Kostoľany
Slovakia
IČO: 44218605
DIČ: SK 2022628102
Read our Privacy Policy.
Head of powder coating operation:
Marián Schwarzbacher
phone (SK): +421 948 403 556
phone (AT): +43 664 2444932
e-mail: vyroba@qkomaxit.sk
CEO of the company
Miroslav Filin
phone: +421 905 576 179
e-mail: filin@qcompany.sk
CEO of the company
Ing. Alexander Kačinec
phone: +421 918 461 504
e-mail: kacinec@qcompany.sk